Specialist Suggestions on What is Porosity in Welding and Just How to Resolve It
The Science Behind Porosity: A Comprehensive Guide for Welders and Fabricators
Recognizing the detailed mechanisms behind porosity in welding is crucial for welders and makers pursuing remarkable craftsmanship. As metalworkers look into the midsts of this sensation, they uncover a globe regulated by various factors that affect the formation of these minuscule gaps within welds. From the structure of the base products to the details of the welding procedure itself, a plethora of variables conspire to either worsen or ease the presence of porosity. In this thorough guide, we will certainly unwind the science behind porosity, discovering its results on weld top quality and unveiling advanced techniques for its control. Join us on this trip through the microcosm of welding blemishes, where precision meets understanding in the quest of flawless welds.
Understanding Porosity in Welding
FIRST SENTENCE:
Evaluation of porosity in welding exposes crucial understandings right into the honesty and quality of the weld joint. Porosity, characterized by the presence of tooth cavities or spaces within the weld steel, is a typical worry in welding procedures. These gaps, if not correctly dealt with, can compromise the architectural honesty and mechanical buildings of the weld, leading to potential failures in the finished product.
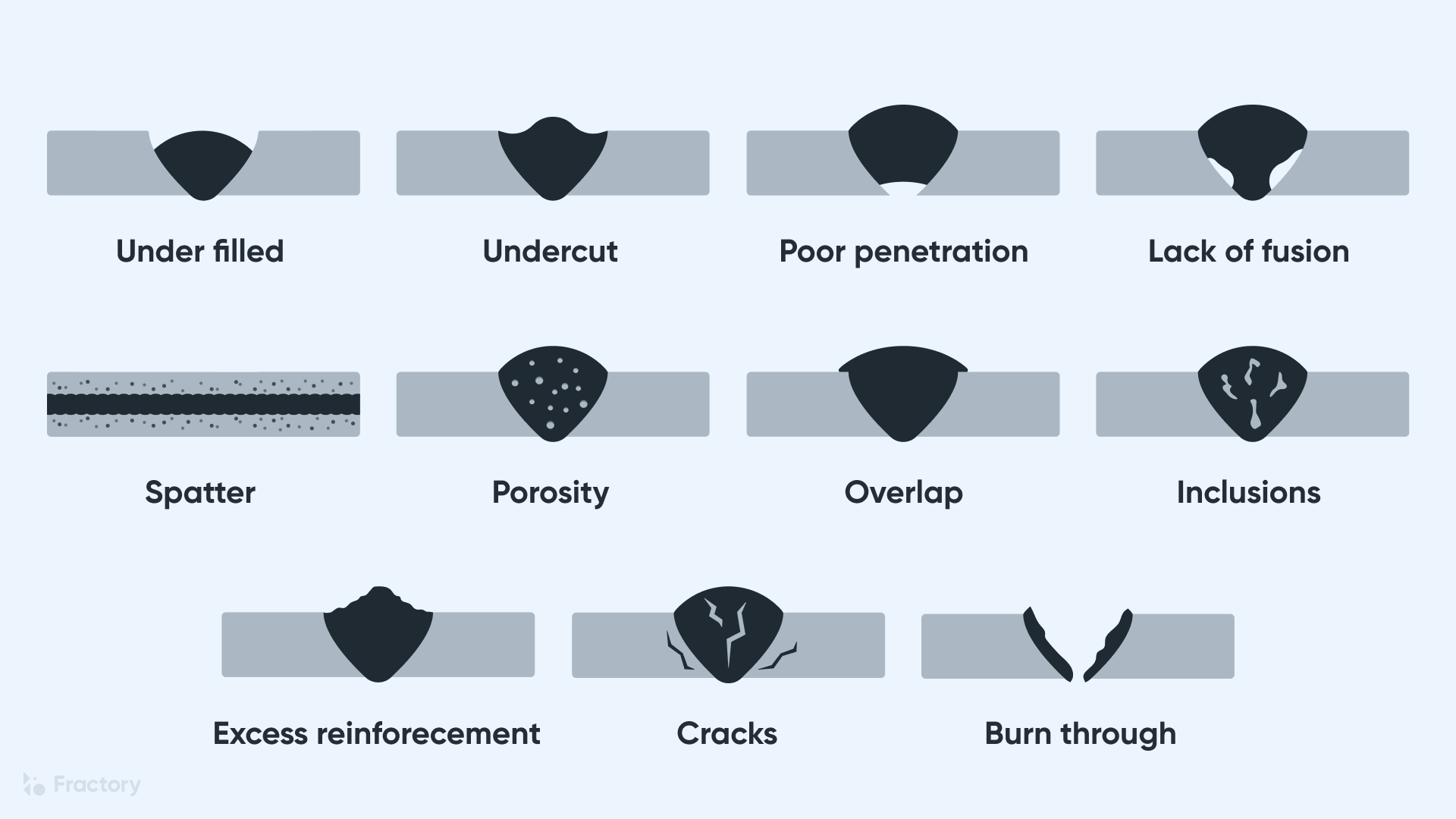
To identify and quantify porosity, non-destructive screening methods such as ultrasonic screening or X-ray examination are frequently employed. These techniques enable the recognition of interior flaws without jeopardizing the stability of the weld. By assessing the dimension, form, and distribution of porosity within a weld, welders can make informed choices to boost their welding processes and attain sounder weld joints.
Aspects Influencing Porosity Formation
The incident of porosity in welding is influenced by a myriad of variables, ranging from gas shielding effectiveness to the complexities of welding specification settings. One important aspect contributing to porosity formation is poor gas protecting. When the protecting gas, generally argon or carbon dioxide, is not properly covering the weld pool, climatic gases like oxygen and nitrogen can infect the molten metal, bring about porosity. Furthermore, the tidiness of the base materials plays a substantial duty. Impurities such as rust, oil, or moisture can vaporize throughout welding, producing gas pockets within the weld. Welding parameters, consisting of voltage, existing, take a trip speed, and electrode kind, also influence porosity formation. Using inappropriate settings can generate too much spatter or heat input, which subsequently can lead to porosity. Furthermore, the welding strategy employed, such as gas metal arc welding (GMAW) or secured metal arc welding (SMAW), can affect porosity formation as a result of variations in warmth distribution and gas coverage. Comprehending and regulating these aspects are important for decreasing porosity in welding procedures.
Impacts of Porosity on Weld Quality
The presence of porosity also damages the weld's resistance to rust, as the caught air or gases within the voids can react with the surrounding atmosphere, leading to degradation over time. Furthermore, porosity can impede the weld's ability to withstand stress or effect, further endangering the overall top quality and reliability of the bonded structure. In critical applications such as aerospace, automotive, or architectural buildings, where security and toughness are vital, the damaging effects of porosity on weld quality can have severe repercussions, stressing the relevance of minimizing porosity through proper welding techniques and treatments.
Techniques to Minimize Porosity
To enhance the quality of bonded joints and make sure architectural honesty, welders and fabricators employ specific techniques targeted at minimizing the formation of spaces and cavities within the material throughout the welding procedure. One efficient method to lessen porosity is to ensure proper product prep work. This includes detailed cleaning Going Here of the base steel to eliminate any contaminants such as oil, oil, or wetness that description can contribute to porosity formation. Furthermore, utilizing the appropriate welding specifications, such as the appropriate voltage, current, and take a trip rate, is essential in avoiding porosity. Preserving a regular arc size and angle throughout welding additionally helps in reducing the probability of porosity.

Utilizing the appropriate welding strategy, such as back-stepping or utilizing a weaving movement, can likewise help distribute warmth uniformly and decrease the opportunities of porosity development. By carrying out these strategies, welders can efficiently lessen porosity and create top quality welded joints.

Advanced Solutions for Porosity Control
Executing cutting-edge modern technologies and cutting-edge approaches plays a pivotal duty in accomplishing exceptional control over porosity in welding procedures. One advanced option is using advanced gas blends. Protecting gases like helium or a combination of argon and hydrogen can assist decrease porosity by supplying much better arc stability and boosted gas protection. Additionally, employing sophisticated welding techniques basics such as pulsed MIG welding or modified ambience welding can additionally aid mitigate porosity issues.
An additional advanced option involves using advanced welding devices. Using tools with built-in functions like waveform control and innovative power resources can enhance weld top quality and reduce porosity threats. The implementation of automated welding systems with exact control over specifications can considerably minimize porosity flaws.
Additionally, including sophisticated surveillance and evaluation modern technologies such as real-time X-ray imaging or automated ultrasonic testing can assist in discovering porosity early in the welding procedure, permitting instant corrective actions. On the whole, incorporating these sophisticated options can significantly enhance porosity control and boost the general high quality of welded components.
Conclusion
In verdict, comprehending the scientific research behind porosity in welding is vital for welders and producers to produce top quality welds - What is Porosity. Advanced solutions for porosity control can better boost the welding procedure and guarantee a solid and dependable weld.